Top 5 Trends Impacting the Manufacturing Market
- Published:Feb 13, 2025
- ●
- Category:White Paper
- ●
- Topic:Life SciencesNutraceuticals & SupplementsAnimal Health, Nutrition & FeedDigital TransformationFood & BeverageSecurity & Compliance
As we enter an era where manufacturing stands at the crossroads of tradition and innovation, the industry is experiencing a shift that promises to redefine its very foundations. As we venture into 2025, manufacturers face a critical choice: embrace the wave of technological advancement or risk being left behind in an increasingly competitive landscape. From AI-powered systems that can predict equipment failures before they occur to cloud-based platforms that seamlessly connect global operations, the manufacturing sector is witnessing a transformation that extends far beyond mere automation. The convergence of digital innovation, supply chain resilience, and customer-centric approaches is creating unprecedented opportunities—and challenges—for organizations ready to adapt. Here's how five pivotal trends are reshaping the future of manufacturing, and why they demand our attention now more than ever.
Digital Transformation via Cloud-Based Systems
Digital transformation is expected to have a major impact on organizational strategies in 2025. It’s significantly reshaping regulated manufacturing industries and fundamentally changing operational processes and customer experiences by leveraging systems that enable real-time monitoring, predictive analytics, and automation among other key functionality. As more manufacturers take a digital-first approach, cloud-based MES platforms are being used to fill the gaps that paper and legacy systems leave behind. These smart systems provide crucial scalability, accessibility, and cost-efficiency advantages that are vital for modern digital initiatives.
Digital technologies will continue to not only improve efficiency, ensure quality, and reduce human error, but it will also allow manufacturers to remain agile and responsive to customer needs. Digital, cloud-based MES platforms have the added benefit of sharing data and connecting sites and teams globally in order to standardize processes and workflows and ensure consistent production practices across locations. These systems also offer advanced analytics and reporting capabilities, allowing manufacturers to have visibility and therefore actionable insights from their data for continuous process improvement.
AI-Powered MES Platforms
If there's one area set to revolutionize manufacturing it would be AI. Artificial intelligence has become an integral part of MES, playing a transformative role in optimizing production processes, improving efficiency, reducing costs, and enhancing product quality. AI-powered MES systems go beyond basic process automation with features that enable manufacturers to optimize production in new ways. The integration of AI technologies in manufacturing is expected to be a critical factor in staying competitive, innovative, and sustainable.
In-demand AI Tools for 2025:
AI Procedure Generation: create procedure templates from prompts or convert existing PDFs with a single click to speed up authoring of procedure templates.
AI Procedure Author Assistant: an author companion that helps modify and optimize procedures during the creation and editing process.
AI Legacy Procedure Migration Tool: Import procedures from a legacy Manufacturing Execution System (MES), in order to streamline digital transformation.
AI Co-pilot: execution co-pilot that provides real-time insights and answers during procedure execution
AI Procedure Recommendations: provides procedure authors with the tools they need to make continuous improvements in order to optimize future batch runs.
AI Procedure Run Summary: offers clear insights into completed procedure runs at a glance.
“Gen AI–based virtual assistants will help optimize drug manufacturing. Potential impact: A 10 to 15 percent improvement in overall equipment effectiveness (OEE) by reducing key losses; a 30 percent–plus increase in productivity for line leaders; a 15 to 35 percent workload reduction for maintenance technicians; a 5 percent reduction in quality costs through the detection of anomalies”
– Source: McKinsey
By leveraging AI, your MES platform can optimize execution, identify patterns, detect anomalies, and facilitate predictive maintenance. What’s unique about AI-powered MES systems is their ability to adapt to changing conditions, continuously optimize processes, and make intelligent decisions that help improve overall manufacturing performance. As a result, product quality remains consistent, downtime is reduced and resources can be allocated more efficiently. Adopting AI-driven MES platforms early on can give manufacturers a significant competitive edge.
In a recent Deloitte survey, roughly 60% of executives cited gen AI or digital transformation as key emerging trends they are closely monitoring. Gen AI investments continue to increase across the industry, suggesting that companies are moving beyond pilot projects and are beginning to realize substantial value from adopting these technologies at scale.
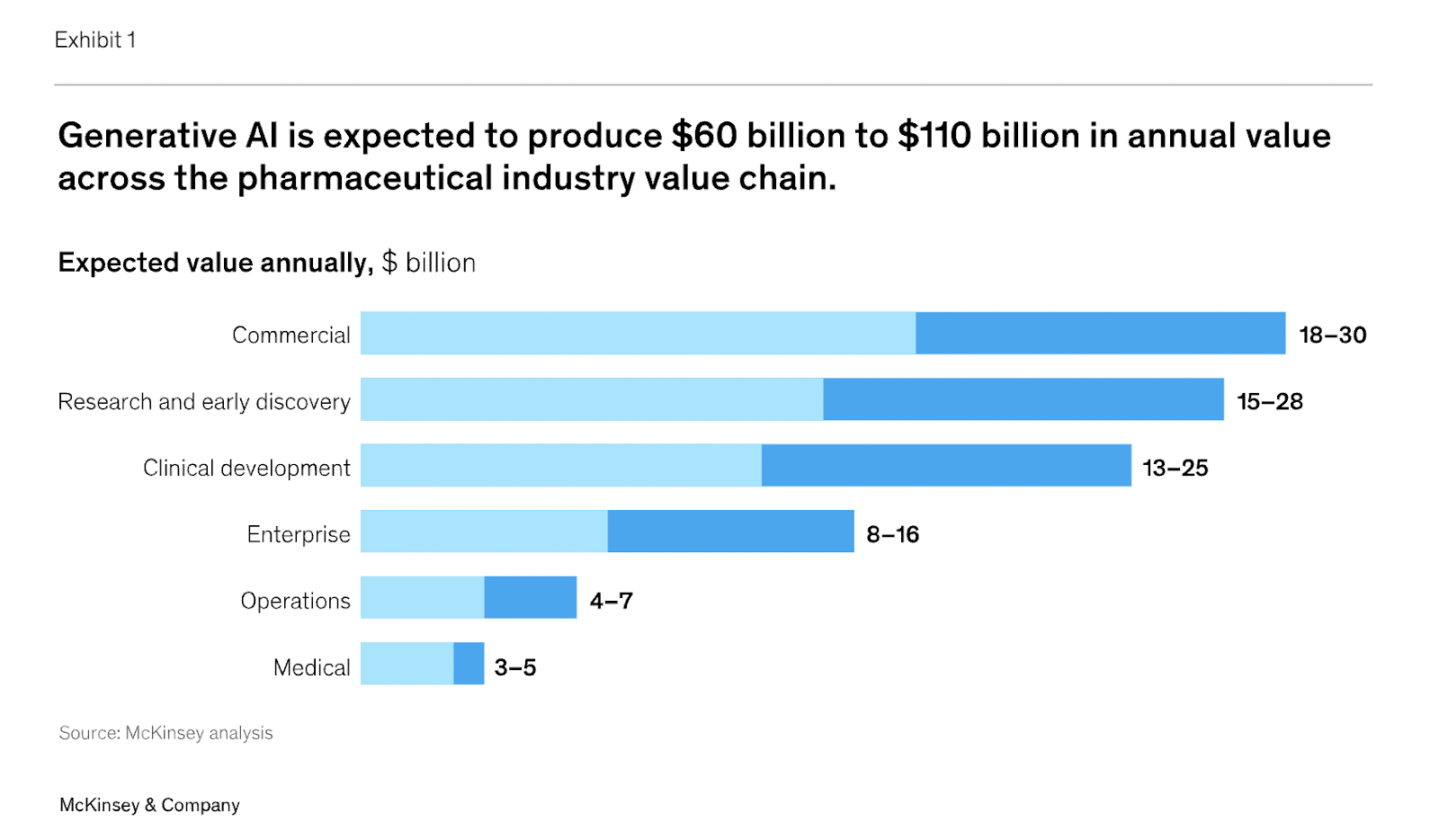
Fortifying & Optimizing the Supply Chain
Supply shortages, geopolitical changes, and natural hazards can all negatively impact manufacturing supply chains. As a result, critical products, specialized materials, and the daily medicines we rely on could be significantly delayed due to raw material shortages, quality issues, or clearance delays. Heading into 2025, evolving global challenges, along with the adoption of manufacturing innovation and heightened regulatory expectations will become catalysts for strengthening the supply chain.
Pharmaceutical Manufacturing, for example, relies on suppliers of raw materials, contract manufacturers, distributors, and logistics. With personalized medicine, biologics, and gene therapies gaining momentum, the pharmaceutical supply chain will become more complex as these therapies require customized production processes and faster turnaround times from lab to patient. As a result, manufacturers will increasingly prioritize the building of a more resilient and adaptable supply chain.
Looking ahead, supply chain models will need to support real-time inventory management and adaptive manufacturing capabilities. In turn, this will lead manufacturers to rely heavily on digital MES platforms that can adapt to fluctuating demands, inject automation into processes, offer up data insights, and help scale production rapidly. MES platforms with built-in AI will also prove invaluable in helping to mitigate risks associated with supply chain disruptions, with the capability to predict shortages and disruptions before they happen. Strengthening the supply chain will be crucial for ensuring that consumers can trust the quality, availability, and origin of pharmaceutical products.
Strengthening Cybersecurity
As more regulated industries go digital, integrating key technologies such as Internet of Things (IoT), automation, and AI into production lines, there’s a greater need for organizations to evaluate their cybersecurity. Furthermore, software and service vendors should have a transparent security framework and be responsible for maintaining safe, verifiable, and auditable processes.
Maintaining data integrity becomes critical for ensuring the trust of both regulatory bodies and the public.Cybersecurity threats will continue to evolve and AI-powered attacks, advanced persistent threats (APTs), and supply chain compromises are expected to increase into 2025. Regulated industries, such as pharma, will need to stay ahead of these evolving threats by adopting next-gen manufacturing platforms that can support proactive measures, zero-trust architectures, and continuous monitoring that detects and mitigates risks. The resilience of pharmaceutical manufacturing operations will depend on their ability to maintain a strong cybersecurity posture.
Despite the challenges, cloud-based MES is becoming essential for modern manufacturers. With proper validation and security measures, these platforms offer a safe, compliant, and scalable solution that encourages drug and product innovation while adhering to regulatory standards.
A Customer-focused Approach
Customer preferences and expectations are likely to shape manufacturing strategies in 2025 and beyond. Life sciences companies in particular must navigate increasingly complex relationships across a wide range of customers, throughout the product development process.
As a result, personalizing the customer experience, establishing trust through transparency, and increasing early engagement will be significant factors for organizations this year.
Evolving customer relationships will become a noticeable trend that C-suite executives will look to improve through the use of more collaborative, data-rich digital systems. As a result, those digital systems will need to be capable of harmonizing data from various customer sources, integrating with other technology systems, and connecting sites and teams all under one platform.
“90% of manufacturers are embracing data-driven approaches to refine CX strategies and optimize resource allocation, driving continuous improvement and innovation.”
–source: Medium
AI-powered MES systems in particular will enable organizations to uncover operational trends for customers, forecast future demands that can usher in growth, and improve quality that leads to greater product consistency, all of which improves the customer experience. Next-gen technologies like cloud-based MES systems can accelerate manufacturing and adjust to changing product specifications, which allows for greater responsiveness to customer needs.
Conclusion
We see 2025 as a pivotal inflection point, where digital transformation is no longer just a competitive advantage—it's becoming a prerequisite for survival. As AI-powered MES platforms demonstrate unprecedented capabilities in optimizing operations and enhancing customer experiences, the question is no longer whether to digitally transform, but how quickly organizations can adapt. Manufacturers must now take decisive action: assess their current digital maturity, identify critical gaps in their technological infrastructure, and develop comprehensive strategies that embrace cloud-based solutions and AI adoption. Those who move swiftly and strategically to implement these emerging technologies will not only weather the challenges ahead but will help shape the future of manufacturing itself. The cost of inaction—in terms of lost efficiency, market share, and competitive advantage—far outweighs the investment required for transformation. As we move deeper into 2025, the message is clear: evaluate your digital transformation roadmap today, or risk falling behind tomorrow.