Top 10 Best MES Features for Pharma
- Published:Feb 28, 2024
- ●
- Category:White Paper
- ●
- Topic:Life Sciences
Executive Summary
Cloud-native Manufacturing Execution Systems (MES) play a critical role in modern manufacturing by offering flexibility, scalability, and real-time insights that translate into significant cost-savings and improved compliance. By design, these modern systems are better equipped than legacy systems or paper-based methods to meet the evolving demands of the pharma industry. They offer up unique features and capabilities that, enhance the user experience, streamline processes, improve compliance and solve problems faster.
Apprentice’s Tempo Manufacturing Cloud, for example, offers an all-in-one, compliant platform that streamlines and speeds up manufacturing processes across the production lifecycle. Tempo integrates seamlessly across manufacturing multiple functions, and is engineered to cover a wide array of manufacturing use cases, harmonizes workflows, enhancing efficiency and reducing the risk of errors.
This white paper will explore the top 10 most desired MES features that are shaping today’s pharmaceutical landscape.From greater efficiency and productivity to process optimization, here are the most innovative Tempo MES features responsible for enhancing connectivity and enabling agile responses to market demands.
#1: Designer Mode
Designer Mode, which is exclusive to Apprentice’s Tempo Manufacturing Cloud platform, allows a user to test run an EBR design and suggest new steps and action inputs directly to the EBR configuration while running and testing the design. This allows for a faster and more direct process knowledge transfer from manufacturing to the EBR author during the configuration stage. This feature is a top favorite among MES engineers as it eliminates the guesswork from EBR configuration thanks to real-time design feedback. This enables rapid iteration and refinement of designs, which leads to faster development cycles and, ultimately, better end products. Stakeholders such as clients, colleagues, and end-users can provide direct input through the designer, fostering collaboration and ensuring that designs align with the vision, requirements, and expectations of all parties involved. More streamlined collaboration means customers can also expect to save critical time and reduce the risk of miscommunication throughout the process.
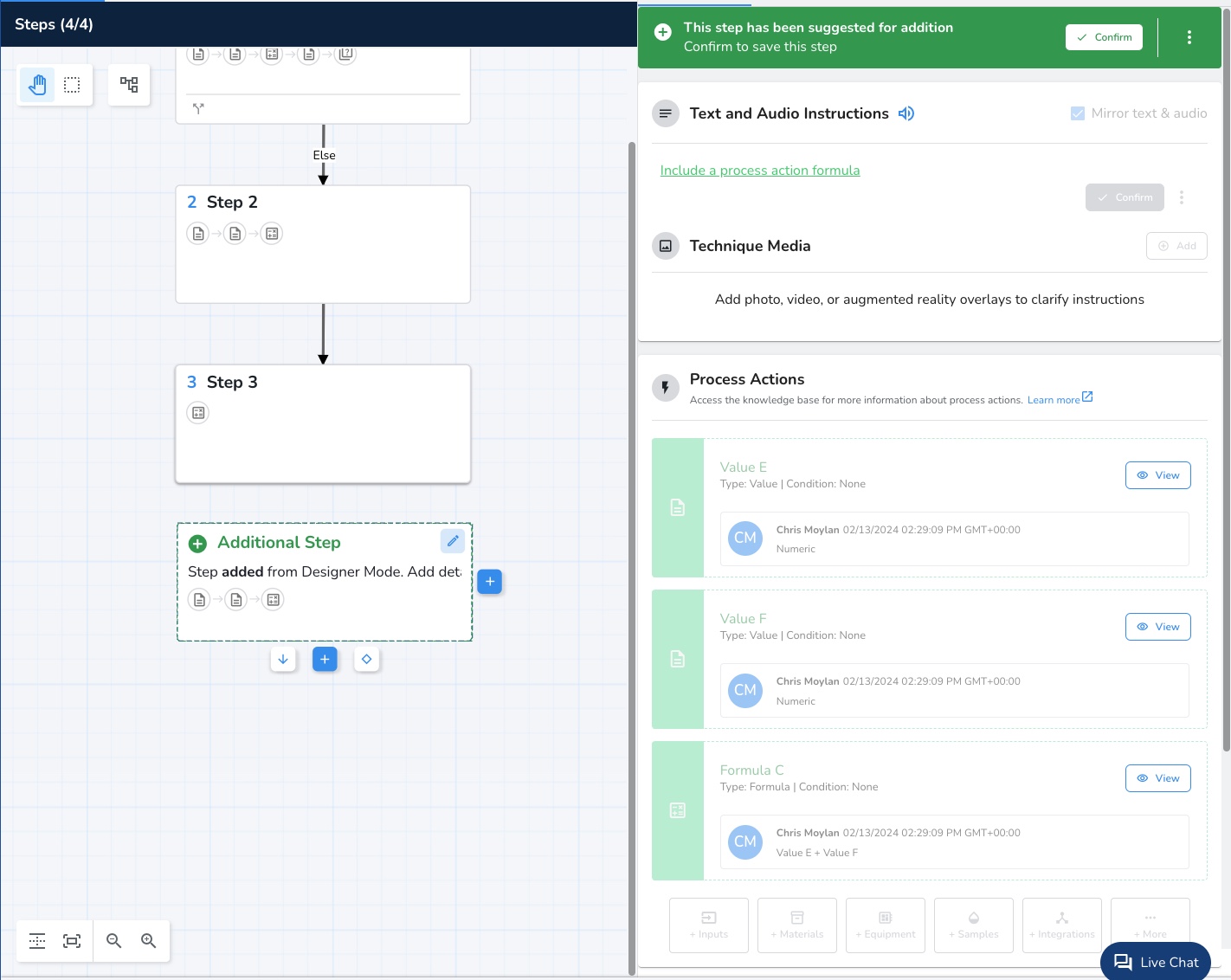
Feature benefits include:
- Improved Design Quality: With the ability to receive immediate feedback, designers can identify and address issues or supply potential improvements early in the process. This leads to higher-quality designs that are more likely to meet user needs and achieve project objectives.
- Better Decision-Making: Access to direct feedback empowers designers to make informed decisions throughout the design process. By considering input from various stakeholders, designers can make adjustments that better meet project goals, user requirements, and industry standards.
- Increased Stakeholder Engagement: Providing stakeholders with the opportunity to give direct feedback on designs enhances their engagement and investment in the project. This fosters a sense of ownership and collaboration, leading to better overall project outcomes.
#2: Remote Assistance
Remote assistance can bring significant value to the pharmaceutical manufacturing process by enhancing efficiency, ensuring quality, and optimizing operations through real-time decision-making and support. This feature allows manufacturing operators to remotely call for QA/Supervisor support directly from the Electronic Batch Record (EBR) execution. Our in-house video collaboration tool, Tandem Virtual Collaboration (TVC) provides remote assistance and remote verification through Tempo, enabling equipment vendors and experts to provide real-time troubleshooting support to on-site technicians or operators. This minimizes downtime and reduces the risk of production delays, equipment failures, process deviations and compliance issues, before they escalate, which minimizes the impact on production schedules and product quality. In addition, remote assistance fosters cross-functional knowledge sharing that can boost innovation. Subject matter experts (SMEs) can connect with teams, regardless of geographical location, providing guidance on critical processes, equipment setup, maintenance procedures, and compliance requirements, ensuring that operations run smoothly and in accordance with regulatory standards.
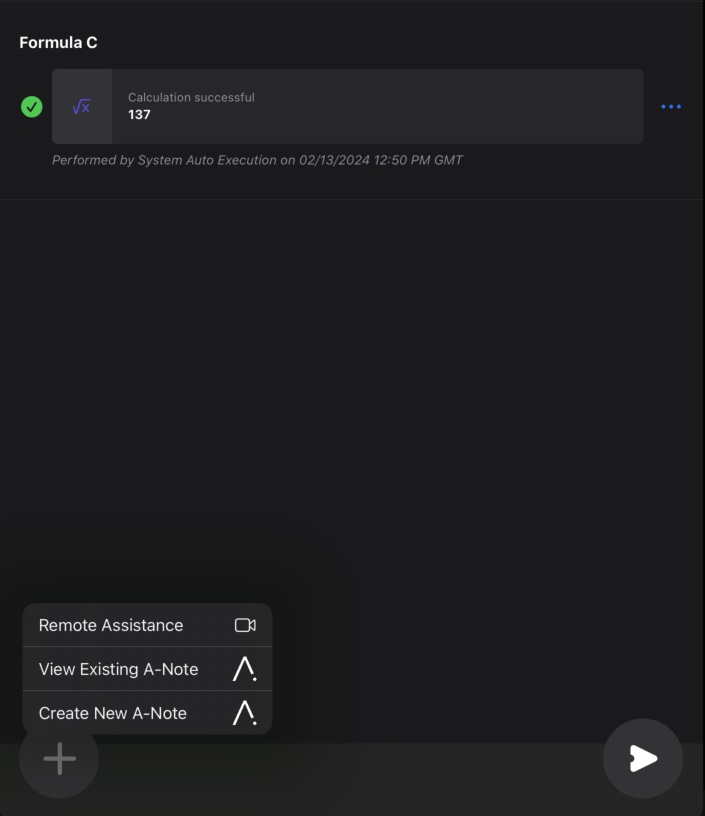
Feature benefits include:
- Faster Training and Onboarding: Remote assistance platforms can be utilized for remote training and onboarding of new staff members, allowing pharmaceutical companies to quickly and efficiently train employees on equipment operation, safety protocols, and good manufacturing practices (GMP) without the need for extensive travel or on-site presence of trainers.
- Improve dQuality: Real-time quality assurance checks can be performed during the manufacturing process. Experts can remotely monitor production parameters, review data, and provide immediate feedback to ensure product quality and compliance with regulatory requirements.
- Reduced Travel Costs and Time: On-demand guidance and live remote support allows companies to minimize the need for on-site travel from SMEs or technicians. This reduces costs, saves valuable time, and allows resources to be reallocated to other critical tasks.
#3: Technique Media
In pharma manufacturing, clear and efficient documentation is key to the overall success of project goals. Through Tempo, our MES customers have the ability to enrich their resources with various multimedia items within the EBR design in order to better document their processes and convey procedural information more accurately. Organizations can streamline communication among cross-functional teams, ensuring alignment and understanding of critical processes and requirements.
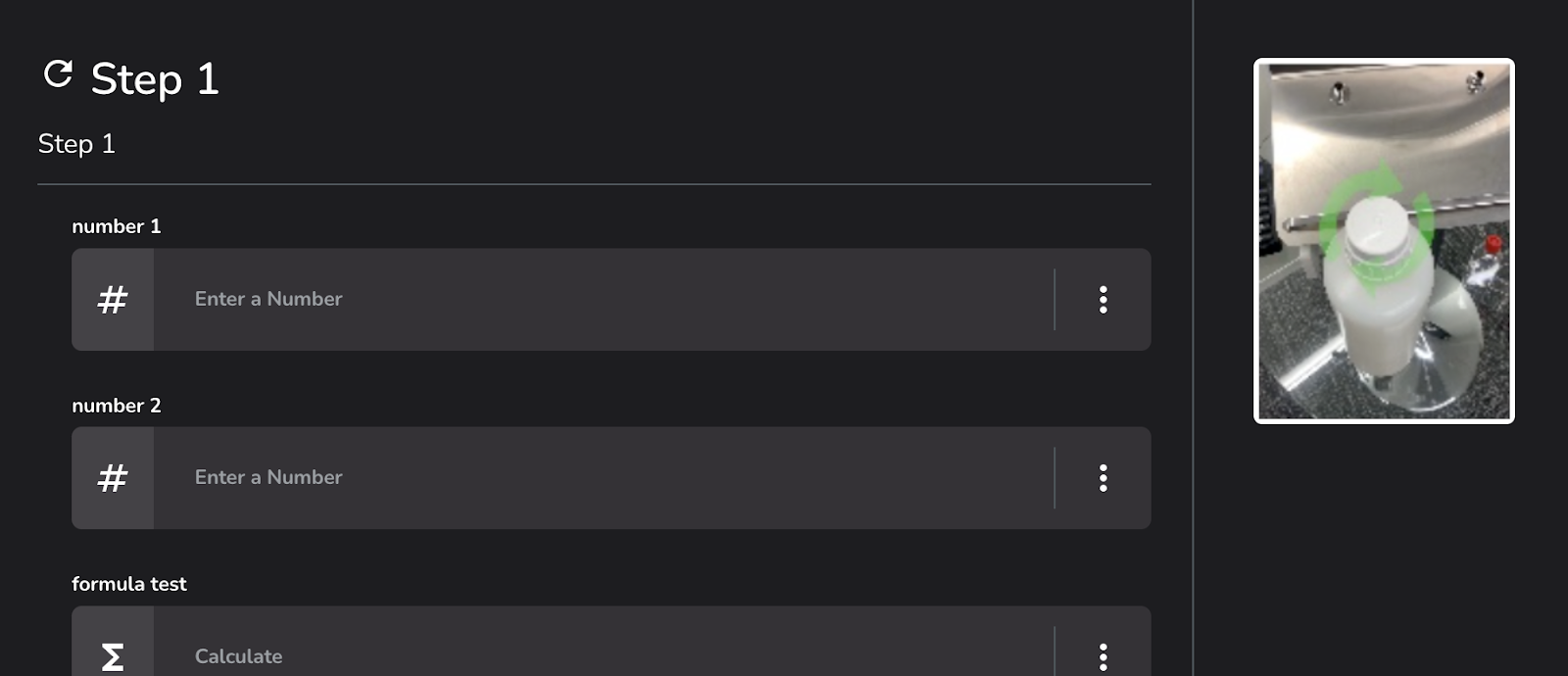
Feature benefits include:
- Enhanced Documentation: Incorporating pictures and videos into EBRs enriches documentation by providing visual evidence of critical steps, processes, and outcomes. This comprehensive documentation ensures greater clarity and accuracy in record-keeping, aiding in audits, compliance, and regulatory inspections.
- Improved Training and Onboarding: Pictures and videos can be used to illustrate complex procedures, equipment setup, and best practices. By including visual aids in EBRs, manufacturers can enhance training and speed up onboarding processes for new employees, contractors, and partners, reducing the learning curve and improving operational efficiency.
- Effective Problem-Solving: Visual documentation facilitates troubleshooting and problem-solving by providing clear visuals of issues, deviations, or abnormalities encountered during manufacturing processes. This helps operators, technicians, and quality assurance personnel to quickly identify root causes and implement corrective actions that can minimize downtime or production disruptions.
- Sustained Compliance: Uploading pictures and videos to EBRs enables thorough documentation of product quality, process deviations, and compliance with regulatory requirements. Visual evidence enhances the integrity and credibility of records, supporting compliance with Good Manufacturing Practices (GMP) and other regulatory standards.
#4: Global Team Objects
If you’re like most of our pharma customers, you are looking for an easy way to leverage the latest cloud-native MES technology to connect everyone in your organization, regardless of geographical location. This is one of the most desired capabilities requested by the industry, making Apprentice’s Global Team Objects feature a favorite. This feature sits within our Connected Manufacturing Network, and allows organizations to connect sites and teams across the globe in a single manufacturing system, fostering greater collaboration and global harmonization.
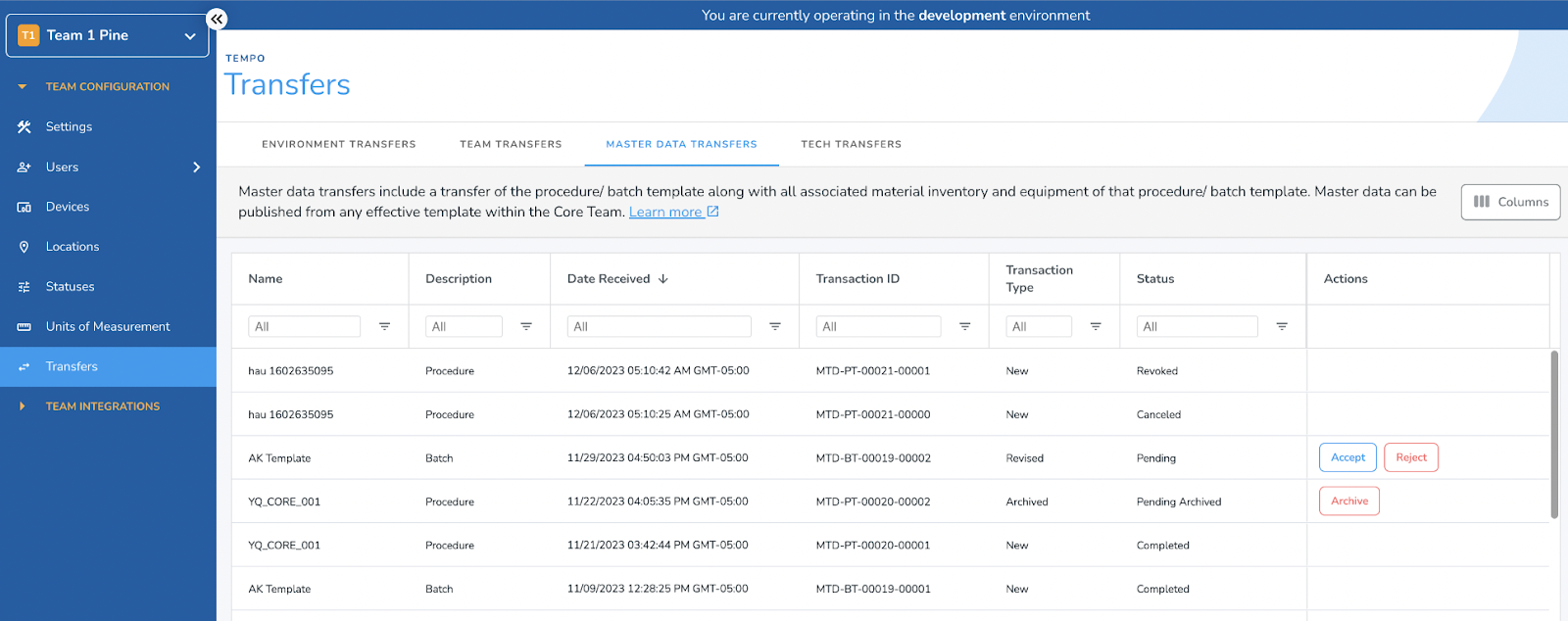
Feature benefits include:
- Centralized Data Management: Centralizing and consolidating data from various sources allos pharmaceutical organizations to standardize and harmonize manufacturing processes across multiple sites or facilities. They can establish standardized protocols, procedures, and specifications, ensuring consistency and uniformity across operations. These “Global Team Objects” become the connective tissue of their process.
- Standardized Workflows and Work Instructions: Digitized work instructions can be disseminated uniformly across all production sites, ensuring that operators follow standardized procedures consistently, leading to improved quality and compliance.
- Cross-Site Knowledge Sharing: By leveraging shared data, best practices, and lessons learned from different manufacturing facilities, organizations can standardize manufacturing processes, optimize performance, and drive continuous improvement across the entire network.
#5: External Customer Review
Having an external customer Electronic Batch Record (EBR) and Exception Review process can provide significant value to a Contract Manufacturing Organization (CMO). These large-scale manufacturers rely on systems that can improve visibility and product quality across their product portfolios. This feature is highly significant among Tempo’s CMO customers and further supports and streamlines commercial production. CMO partners can digitally communicate with, submit, and track batch approvals, ensuring that they can move forward with manufacturing quickly and prepare for new product introductions. With greater visibility into manufacturing processes, and the ability to review and approve exceptions, CMOs can increase overall customer satisfaction and trust.
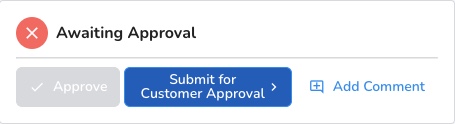
Feature benefits include:
- Greater Transparency: Providing external customers with access to EBRs and Exception Reviews fosters transparency and collaboration between the CMO and its clients. Customers can monitor the progress of their manufacturing projects in real-time, track key performance indicators, and collaborate with the CMO to address any issues or deviations promptly.
- Proactive Corrections: Customers can review and approve critical manufacturing deviations, ensuring that any necessary corrective actions are implemented in a timely manner to maintain manufacturing timelines in addition to product quality.
- Simplified Audits and Inspections: Having an external customer EBR and Exception Review process in place simplifies audits and inspections conducted by regulatory authorities, or customer representatives. Customers can access relevant documentation and audit trails directly, expediting the audit process and demonstrating compliance with regulatory requirements and contractual obligations.
#6: Augmented PDF Builder
Unlike traditional systems, modern, cloud-native MES systems offer users the opportunity to easily enrich and annotate existing content, building upon the digital-first, Pharma 4.0-driven manufacturing ecosystem. Organizations can push their digital goals forward quickly and easily, without having to recreate new content. This feature transforms paper-based processes and improves document usability and enriches workflows.
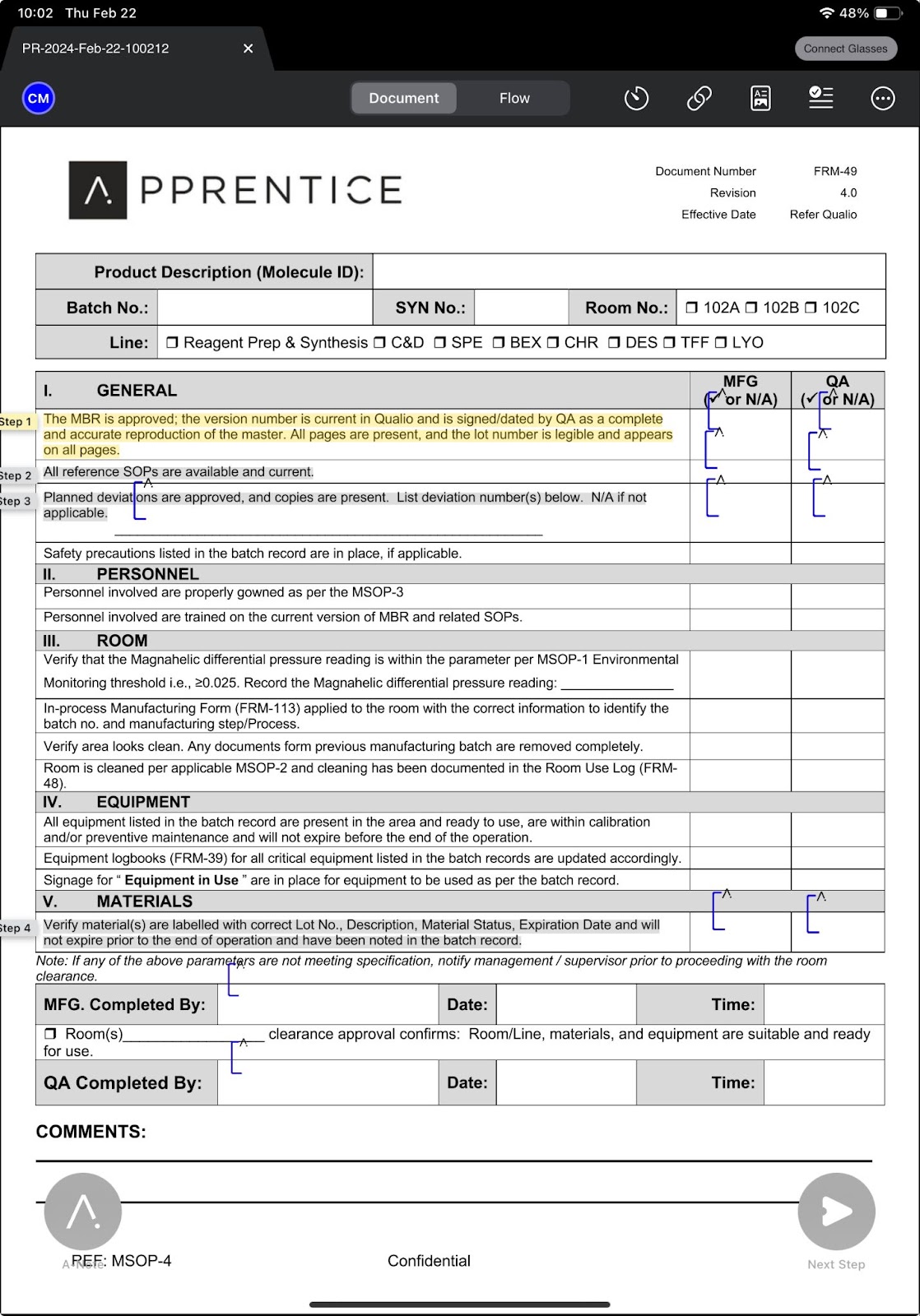
Feature benefits include:
- Enhanced Documentation: Augmenting PDF documents allows you to enrich traditional documents with additional interactive elements such as hyperlinks, multimedia content, annotations, and interactive forms. This enhances the readability and usability of documents, making it easier for users to access relevant information, navigate complex documents, and understand critical concepts.
- Improved Education: Augmented PDF documents can be used for training and education purposes. Companies can create interactive training materials, instructional guides, and educational resources embedded with videos, animations, quizzes, and simulations to enhance learning experiences for employees, healthcare professionals, and patients.
- Accelerated Digital Initiatives: Augmented PDF documents support digital transformation initiatives within the pharmaceutical industry by enabling the transition from paper-based to digital documentation processes. Companies can digitize paper-based documents, forms, and records, augmenting them with interactive features to improve accessibility, usability, and efficiency in document management.
#7: No-Code Integrations
No-code integrations in Manufacturing Execution Systems (MES) are especially valuable for connecting and automating equipment, steps and processes that are otherwise segmented within the pharmaceutical industry. Organizations can easily connect disparate systems and applications to their MES without extensive technical resources or custom coding. This provides immense value and cost savings to organizations looking for end-to-end platforms that can connect all their systems. In addition, no-code integrations are inherently scalable and adaptable to accommodate future growth, expansion, and changes in business needs. Organizations can easily add new integrations, modify existing ones, or scale up their integration capabilities as their operations evolve over time. With a more agile MES in place, organizations can easily adapt to changing business requirements, evolving technology landscapes, and emerging industry standards without the constraints of traditional coding approaches.
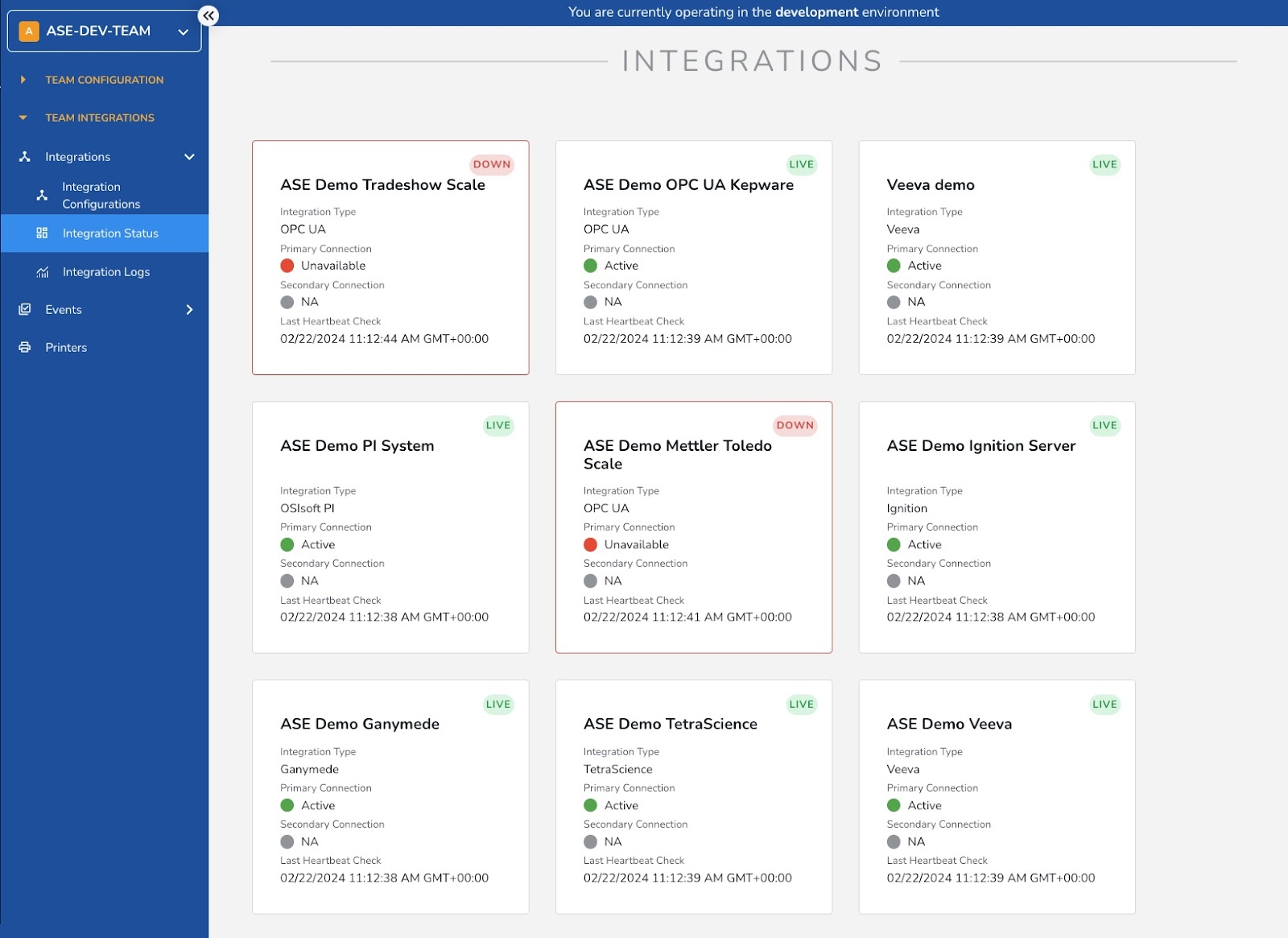
Feature benefits include:
- Empowered Users: Business users and domain experts can create and manage integrations independently, without requiring extensive technical expertise or programming skills. This democratization of integration capabilities enables faster innovation and problem-solving at the operational level while empowering users.
- Reduced Maintenance Overhead: No-code integrations typically have lower maintenance overhead compared to custom-coded solutions. Organizations can easily modify, update, or scale integrations as needed using intuitive visual interfaces, reducing the time and effort required for ongoing maintenance and support.
- Enhanced Data Visibility and Insights: This feature also enables the seamless exchange of data between systems like Tempo and other applications,, providing organizations with a unified view of manufacturing operations and supply chain processes. This enhances data visibility, enables real-time analytics, and facilitates data-driven decision-making across the organization.
#8: Multi-conditional Navigation
Multi-condition step navigation is a dynamic Tempo feature that adds significant value to an Electronic Batch Record (EBR), allowing users to navigate through steps, conditions, or events within the document. Operators are guided through complex “if” “then” scenarios, to streamline batch execution. This feature ensures that procedures are completed quickly and properly, while avoiding deviations and automatically adjusting to changes. Instead of following a linear sequence of steps, operators can dynamically navigate based on predefined conditions, ultimately minimizing the risk of error.
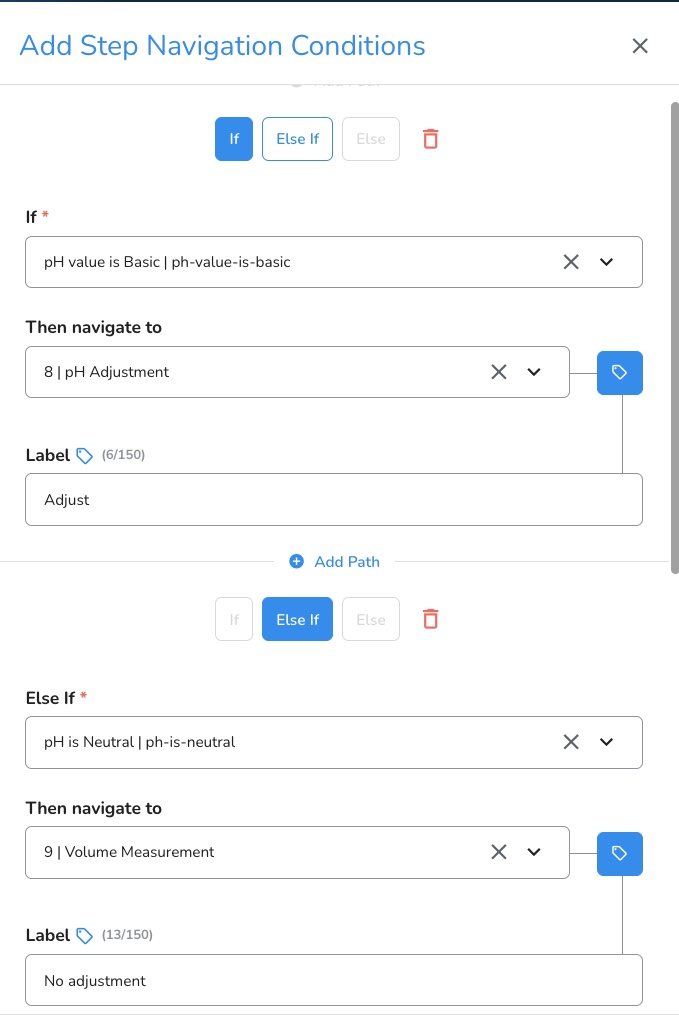
Feature benefits include:
- Greater Flexibility: Variations in manufacturing processes operators navigate through different process paths based on specific conditions such as values, equipment status, or quality attributes, ensuring optimal execution of batch operations.
- Time Savings: Operators can save time by navigating directly to relevant steps based on specific conditions or events, streamlining batch execution and reducing the time required to complete manufacturing processes. This enhances productivity, reduces cycle times, and improves overall operational efficiency in the production environment.
- Improved Compliance : With a guided workflow helping operators through predefined process paths based on process conditions, organizations can minimize the risk of deviations, ensure consistency in process execution, and enhance quality assurance across the batch lifecycle.
#9: Multiple EBR Designs
Tempo offers three unique EBR design options that encourage greater flexibility and scalability for template design. These modes include Augmented PDF Builder, List Builder and Visual Builder. Each one provides a specific design method tailored to the user’s operational approach, whether they are starting from an existing paper procedure, or building complex SOPs.
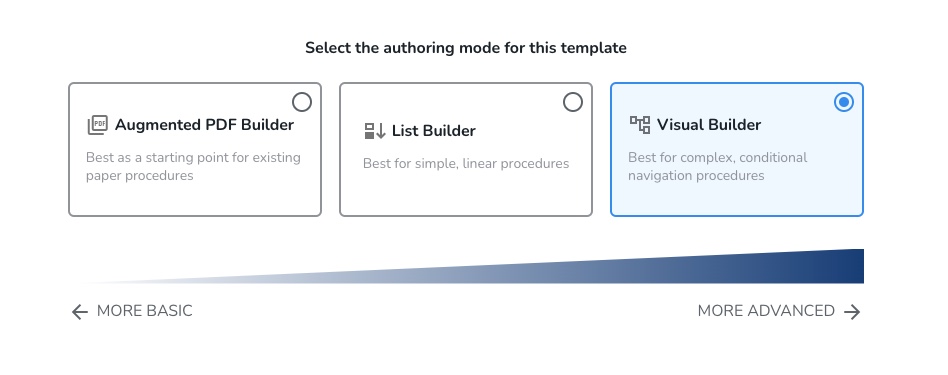
Feature benefits include:
- Greater Flexibility: Offering multiple design options allows Tempo to cater to different manufacturing environments, processes, and user preferences. This flexibility enables companies to adapt the system to their specific needs without extensive redevelopment.
- More Customization: Each design option can cater to different levels of customization, providing users with the ability to tailor the MES interface and functionalities to better align with their workflows and business requirements. This customization can enhance user satisfaction and overall productivity.
- Easy to Scale: With multiple design options, the MES system can scale more effectively as the company grows, or changes. Different design options can accommodate varying levels of complexity, volume, or integration needs, ensuring that the system remains effective and efficient regardless of the scale of operations.
#10: Mobile Execution App
Having multiple device options available to use with MES software can offer teams greater operational flexibility across various work environments, in accordance with their technology preferences. Tempo users can execute digitally on iPad, web browser, or a hands-free headset, depending on the use case and operator preference. This feature allows teams to remain agile and comfortable as they execute.
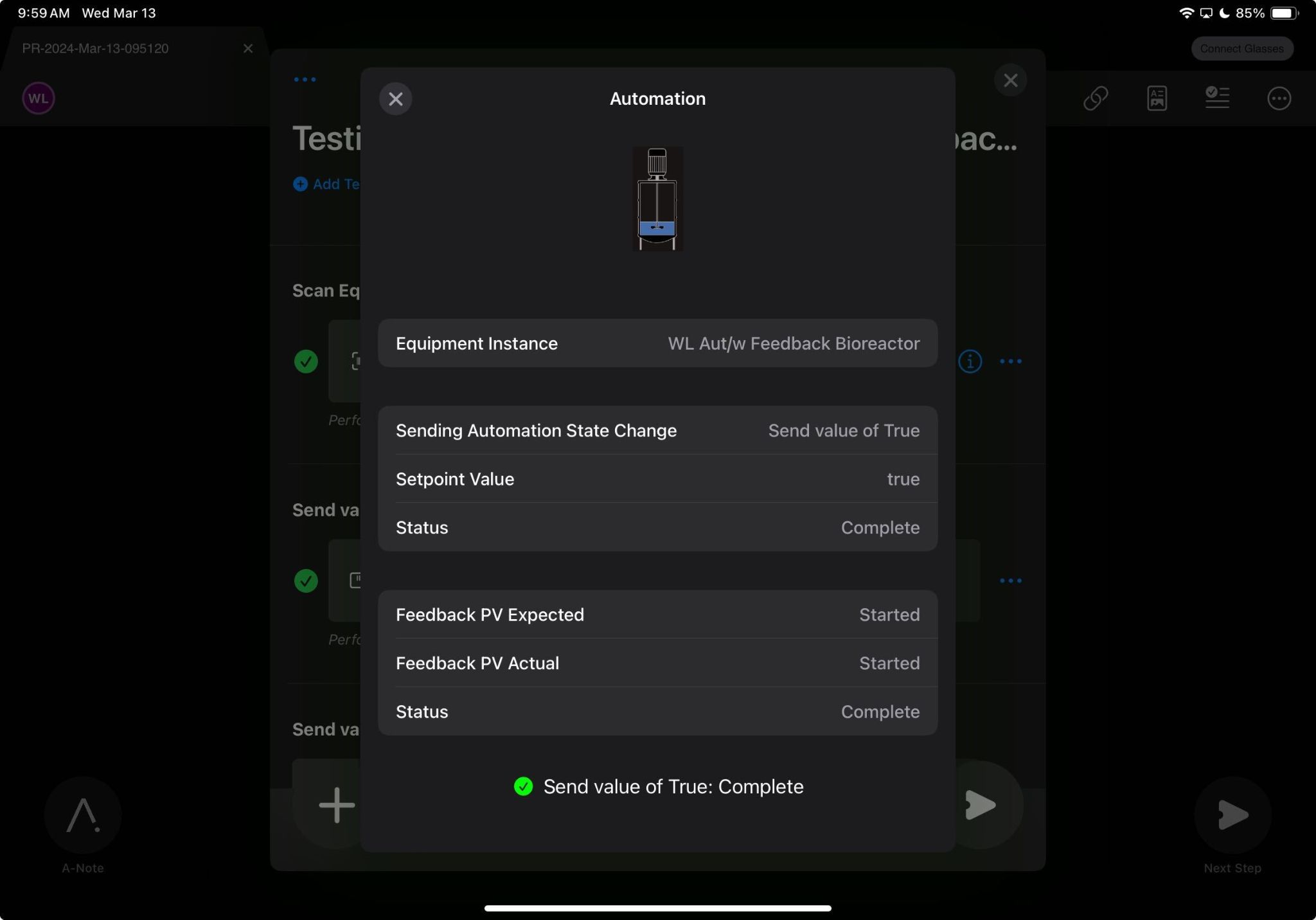
Feature benefits include:
- Improved Comfortability: Different users may have preferences for devices they are comfortable working with, whether it's a tablet, hands-free headset that leverages voice commands, or a web-based browser. Offering compatibility across these platforms allows users to access Tempo from their preferred device, enhancing flexibility and mobility. This is particularly valuable in manufacturing environments in which users may need to access the system from various locations on the shop floor, or remotely.
- Increased Accessibility: Not all users have access to the same types of devices. Tempo is compatible with tablets, hands-free headsets, and web browsers, making the entire platform more accessible to a broader range of users within the organization. This ensures that all stakeholders, regardless of their device preferences or limitations, can effectively engage with the system.
- Intuitive User Experience: Tablets, hands-free headsets, and web browsers each offer unique interaction methods. Optimizing the Tempo for each of these platforms ensures a consistent and optimized user experience. Whether users are accessing the system on a tablet with a touch screen, using voice commands through a hands-free headset, or accessing it through a web browser, they can enjoy a seamless and intuitive user interface.
Our Featured Thought leader
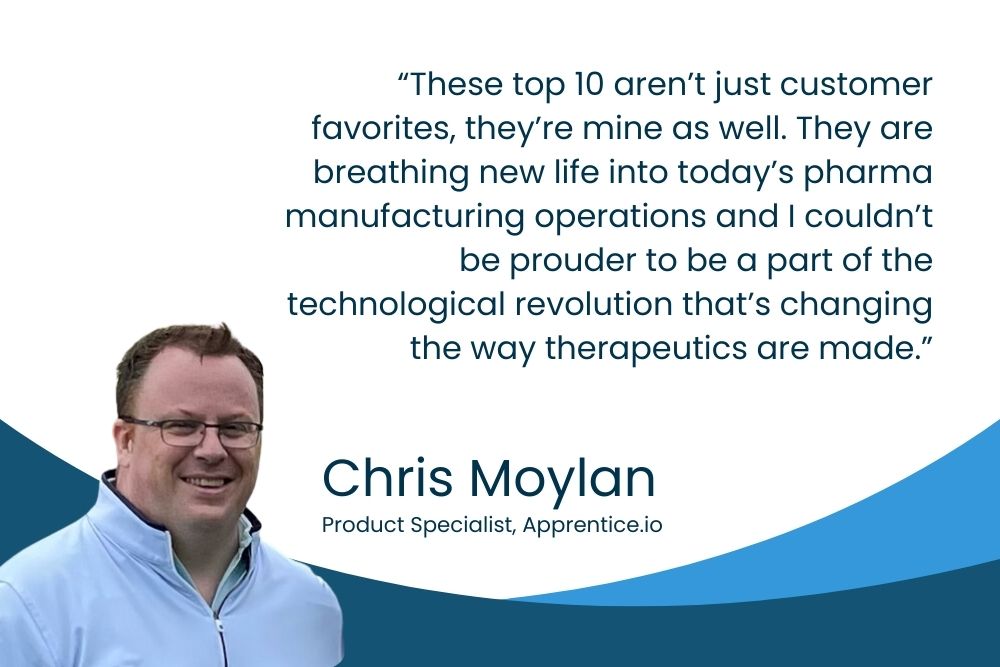
Conclusion
Modern, cloud-native software is a pivotal innovation that is revolutionizing the way industries operate and connect within the full manufacturing network. As far as pharma goes, the combination of these top 10 features within a cloud-based MES provides manufacturers with the tools they need to optimize processes, improve efficiency, and stay agile in a dynamic manufacturing environment. With the ultimate goal of getting therapeutics to patients faster, agile technology is key in remaining competitive. With real-time data analytics, seamless integration capabilities, and intuitive user interfaces, cloud-native MES software empowers manufacturers to optimize operations, improve decision-making, and drive efficiency at every level of their organization. By facilitating collaboration, visibility, and control throughout the manufacturing network, these innovative solutions enable businesses to adapt swiftly to market demands, enhance productivity, and ultimately deliver superior value to customers in today's dynamic and competitive environment.
By harnessing the power of cloud technology, Apprentice's Tempo Manufacturing Cloud, offers unprecedented agility, scalability, and connectivity across production processes, supply chains, and beyond. Tempo saves time, streamlines resources, and boosts efficiency.
Ready to embrace the digital revolution and turn the page from paper-based losses to digital gains? Schedule a demo of Tempo today.