Is It Time to Move On from Your MES Vendor?
- Published:Nov 2, 2023
- ●
- Category:White Paper
- ●
- Topic:Life Sciences
It's a New Era
Manufacturing Execution Systems (MES) are a well-established software used to transform raw materials into a finished drug product. However, these systems were first developed in a different technological landscape than today. On-premise solutions were king, requiring heavy coding for initial development with monumental maintenance and services to match. Today's landscape includes cloud-based solutions, with an emphasis on ease of use paired with low maintenance and services.
MES stands at the core of your plant's manufacturing operations, serving as the linchpin responsible for streamlining and automating your processes. It enables you to orchestrate and track real-time batch production, synchronizing with your Enterprise Resource Planning (ERP) system. This theoretically provides site heads, supervisors, Quality, and other teams with access to a wealth of information for decision-making, as long as you’re not struggling with an antiquated and inadequate MES platform.
Times have evolved, and if this vital component is no longer performing as it once did, it may be time to contemplate a change. In this white paper, we will show you several ways to identify if that time is now.
Signs That It’s Time to Move Forward into a Modern MES
#1: Limited scalability that hinders growth
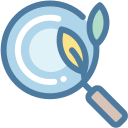
Your MES must be scalable in order to support an organization-wide deployment. Implementing a critical and resource-intensive system like an MES often leads to significant consumption of valuable employee bandwidth, or high costs, if external services are used. When conventional systems are deployed, you can end up with a disconnected set of sites, each with an individualized MES. The future of MES is one in which you can deploy at a new site on the fly and seamlessly connect information between them and to other systems. To optimize resource use and process efficiency, your MES should be deployment-ready today or in the near future.
#2: Your MES is too complicated to have experts
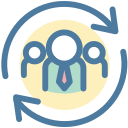
Are there only a few true MES experts? In the past, MES systems were designed with such complexity. This complexity extends beyond coding for customization or deployment; it also affects aspects like recipe creation and maintenance or platform updates. The result? A technical barrier so high that either a few select individuals were experts on the platform, or groups were required to develop expertise in the field. The former method can leave your organization vulnerable to the loss of knowledge due to employee turnover. Meanwhile, the latter leads to high costs from the number of required quasi-experts.
Modern systems are purposefully designed to be intuitive and user-friendly, enabling employees from the shop floor to management to take charge and unlock the benefits of the system without dependency on a singular expert. The goal is to make it user-friendly to the extent that almost anyone could use it effectively.
#3: Your data is inaccessible
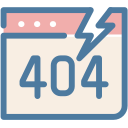
In today's dynamic manufacturing landscape, data collection and accessibility have become critical challenges for organizations still relying on outdated MES systems. Extracting data from both paper and shop-floor equipment is a time-consuming and error-prone process. If it’s coming from paper, each data point has to be manually re-transcribed into a digital system, and humans aren’t known for performing processes perfectly. If it’s from a shop-floor system, equipment, or a traditional MES, the lack of connectivity to other systems means that data still needs to be manually re-transcribed, just from digital-to-digital instead of paper-to-digital. This inflexibility often leads to workarounds when attempting to integrate data from other systems or equipment, if such integration is even possible.
A contemporary MES can address these challenges by offering two different ways to discover and utilize insights. The first is built-in reporting, which can be used ad-hoc to find the required insights. The second, for organizations more mature in their data analysis, involves connecting directly to the data analysis tool preferred by data scientists. Either approach is instrumental in providing decision makers with the information they need to ensure that production is as efficient and high-quality as possible.
#4: Maintenance is starting to add up
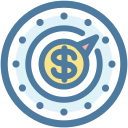
While the age-old adage “If it ain't broke, don't fix it” has its merits, there comes a point where strict adherence to it may be carried to extremes. An outdated MES, especially one that you’re unable to upgrade, leaves you dealing with known bugs, compatibility issues, security vulnerabilities, and the inability to leverage the latest technological advancements essential for adhering to industry best practices. In addition to the functionality perspective, there are ongoing maintenance costs associated with on-premise deployments, which have become obsolete with SaaS.
If your current MES software is years into your current version, and a daunting re-deployment is looming in order for you to access the latest updates, it may be time to bid farewell.
#5: Struggling to keep up with emerging modalities
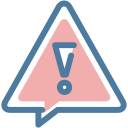
Pharma's landscape is undergoing a significant transformation as it shifts away from conventional small molecule therapies toward cutting-edge biologics and Cell & Gene Therapies (CGT). Biologics sales are growing exponentially, with CGT experiencing its own boom. The momentum in this direction is undeniable, and it's reshaping the manufacturing sector as a result. The manufacturing processes for biologics and CGT are also increasingly complex in comparison to Small Molecule.
A legacy MES can often struggle to perform in these areas. Even simple recipes take time to code and validate with these systems. These new modalities often require high degrees of editability, not only in process development, but in execution itself. The rigid development and structure of a traditional system doesn’t adapt well to these new modalities. During execution, legacy systems can have few to no protective measures around how a step is performed, which means operators can still make many mistakes. Losing a batch of such complexity can be worth hundreds of thousands, or even millions. At sites manufacturing multiple modalities, these issues may be exacerbated to the extent that the MES used to make small molecule drugs cannot be adapted for other modalities, necessitating the use of paper in their place.
#6: It’s literally showing its age
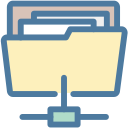
Your MES may be experiencing performance issues. It might be sluggish in responding to commands, unable to handle the required capacity, or more restrictive than empowering. Such performance degradation can hinder productivity and cause delays, ultimately impeding the efficiency of your operations.
Visually, your users can likely tell the system's age as well. From a user-experience perspective, today's users expect their business applications to mirror the seamless experience they have with their own personal technology. An outdated MES may fall short in terms of visual appeal, potentially preventing interactivity, adoption, and ease of use, while creating a gap between user expectations and the system's actual performance.
Simultaneously, we’re seeing newer generations entering the workforce. These generations grew up digital-first; the days of handwriting classes are long gone. In a day and age where finding and retaining talent is as competitive as ever, delivering a user experience in line with the early 2000s, puts your organization at a disadvantage.
Next Steps
If you’re identifying with any of these six points, it might be time to consider a modern MES. These new systems:
- Can start at one site, or with just a single team, but will support deployment to many sites and teams as a single unified platform
- Reduce the complexity of use, aiming to make it easy and intuitive for any user to learn and use for their role from day one
- Connect and extract data from systems and equipment to give you a single source of truth for your manufacturing information
- Deliver the latest features and fixes without any of the maintenance, due to its cloud-native design
- Eliminate the need for coding, and emphasize editability and flexibility especially when it comes to process development
- Prioritize a modern user interface and experience
Think it’s time? Our Tempo Manufacturing Cloud can address these six areas and more.
Contact us to experience the future of manufacturing with Tempo..