10 Tips to Optimize Tech Transfer in Pharma
- Published:Aug 5, 2022
- ●
- Category:White Paper
- ●
- Topic:Life SciencesProduct Insights
Tech transfer in pharma is a difficult, yet often overlooked element of drug manufacturing. Not only does it enable companies to bring drugs from preclinical to clinical to commercial rollout with a single team, on a single site, but it also increases speed and efficiency all the way through.
Welcome to the next installment of our Tech Transfer Deep Dive Series, in which we walk through our ten top tips to make your pharmaceutical tech transfer as seamless and painless as possible.
Missed our first two Tech Transfer papers? You can find them here:
- Part 1: Tech Transfer: First Cookies, Then Pharma
- Part 2: Tech Transfer: From Preclinical to Clinical
Tech Transfer: An Essential Part of Drug Manufacturing
To successfully scale drug development and manufacturing, tech transfer is essential. But it’s also costly, complicated, and time-consuming. Completing a pharma tech transfer requires more than $5 million, a team of experts, and can take from 18 to 30 months.
That hefty price tag doesn’t include the cost of tech and validation of batches — which are necessary to authenticate the processes. The reality is, for most pharma companies, tech transfers are a major headache.
Fortunately, relief is within reach. In this article, we’ll explore tech transfer in detail and outline 10 tips you can take to make it more effective.
Jump to…
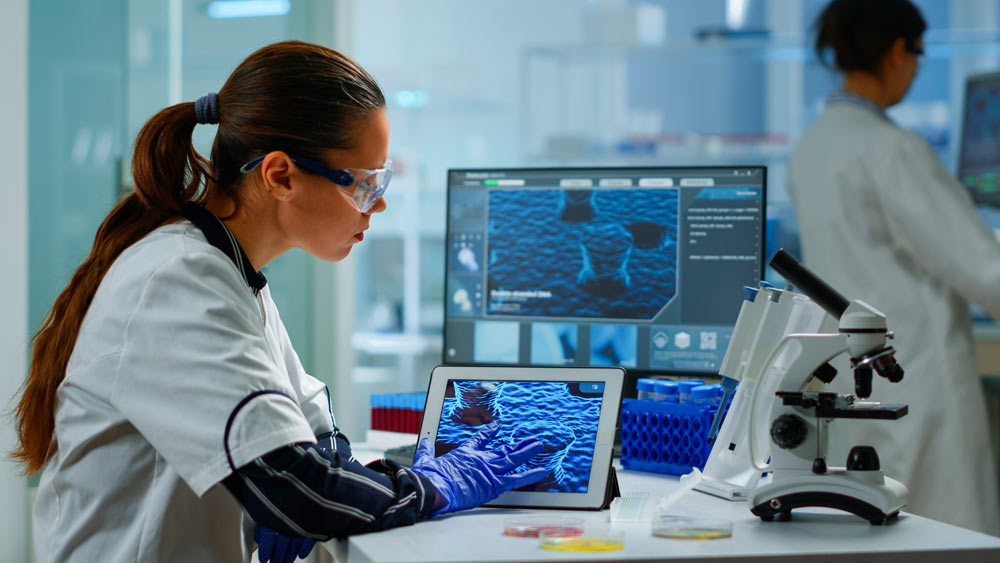
Tech Transfer: An Overview
Before we dive into the specifics of pharma tech transfer, let’s start with a broad definition.
What is tech transfer?
Tech transfer, also commonly referred to as transfer of technology (ToT) or TT, is the sharing of information between governments, businesses, or universities. The information shared often includes manufacturing methods, knowledge, software, intellectual property, technologies, skills, and other data.
There are two primary types of technology transfer, which include:
- Vertical tech transfer: Also known as internal tech transfer, this occurs when information is funneled between research associations, universities, and governments.
- Horizontal tech transfer: This type of transfer, also referred to as external tech transfer, takes place when one organization shares its processes or information with another organization to use. This occurs between private companies and various businesses.
Licensing and joint venture agreements are the two most common examples of tech transfer in action. Tech transfer also plays a major role in industries such as computing, transport, agriculture, aerospace, and robotics.
Why is tech transfer important?
Tech transfer is important because it enables companies, governments, and research institutions to quickly and accurately share necessary information so others can reproduce their processes or build upon them. As a result, novel technologies and products can penetrate the market sooner.
Without tech transfer, organizations wouldn’t be able to replicate a process across teams, sites, or software. Tech transfer bridges the gap between siloed areas of expertise, helping companies stay up to speed on new technologies and industry innovations from their peers.
What is tech transfer in pharma?
In pharma, tech transfer refers to the process of sharing pharmaceutical manufacturing data and knowledge across different teams, sites, and stages of drug development.
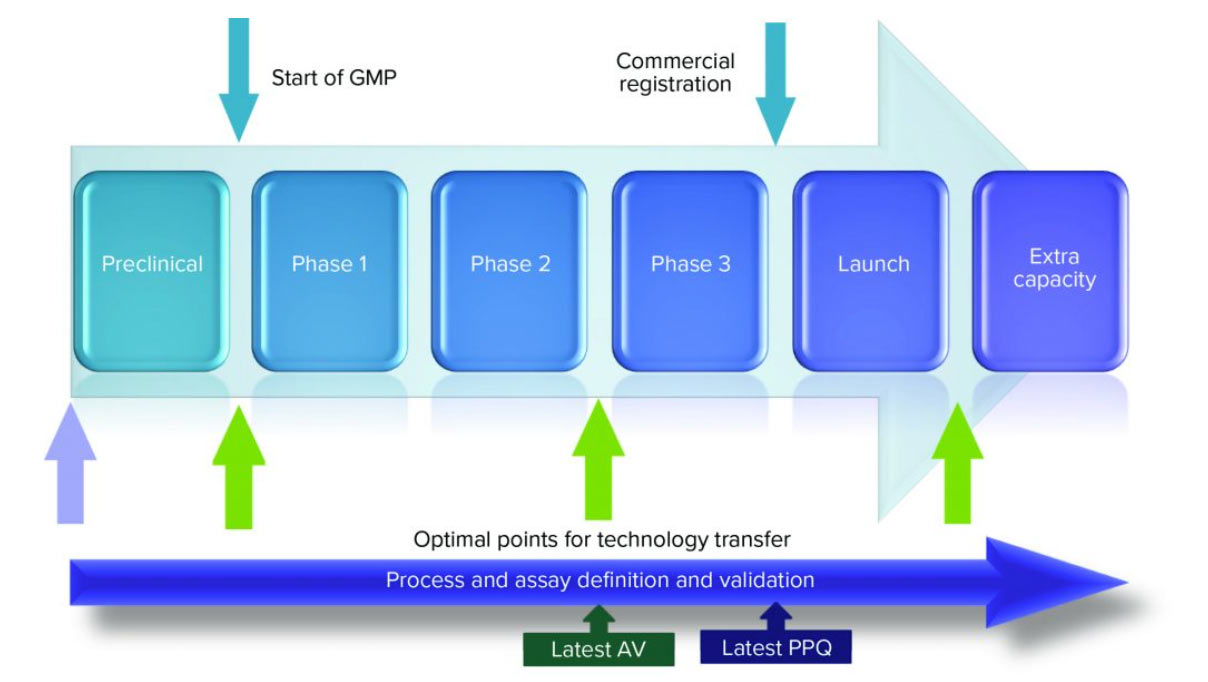
Tech transfer in pharma occurs for a variety of reasons, including:
- Site to site and team to team transfers
- Facility changes
- Company mergers and acquisitions
- Transferring information to contract development and manufacturing organizations (CDMOs) or back in house from CDMOs
Sounds simple, right?
But don’t be deceived by this seemingly straightforward process. In practice, it’s often cumbersome and difficult to successfully package and communicate all the needed data. Forgetting to submit all relevant information to your CDMO, for example, is the equivalent of throwing money into a fire.
At best, the drug manufacturing cycle will be delayed until all of the relevant information is available. At worst, batches may be manufactured incorrectly, resulting in wasted resources and delayed timelines.
Assuming you don’t want to burn your company’s money (and we know you don’t), let’s dive into ten of our top tips to make tech transfer in pharma more effective.
Our Top 10 Tips to Up Your Pharma Tech Transfer Game
Tech Transfer Tip #1: Set Clear Goals
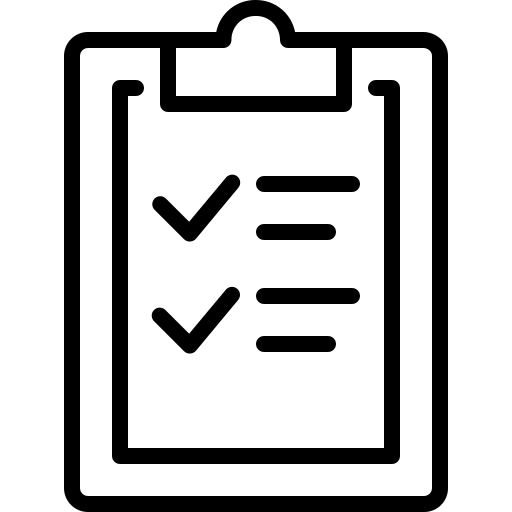
There isn’t a one-size-fits-all approach to success in drug production. As such, our first tip to make your tech transfer more effective is to set clear goals for your pharma organization. The objective here is to align everyone early on, so you can set expectations from the start and minimize any potential misunderstandings.
To aid in your goal-setting and streamline the conversation, you can prepare questions to ask your stakeholders.
Questions to ask include:
- For clinical trials, what’s the optimal phase for us to begin thinking about TT?
- Is our research and preclinical study data organized and easily transferable?
- For scaling up existing drugs, what’s our TT timeline, associated costs, and deliverables?
All these questions should be explored, answered in detail, and shared with relevant stakeholders. Naturally, these questions will vary depending on the purpose of your TT. For example, if your organization is preparing for a tech transfer as part of a therapy currently in clinical trials, your requirements will be different from an organization switching sites or CDMOs.
Tech Transfer Tip #2: Prepare All Relevant Information
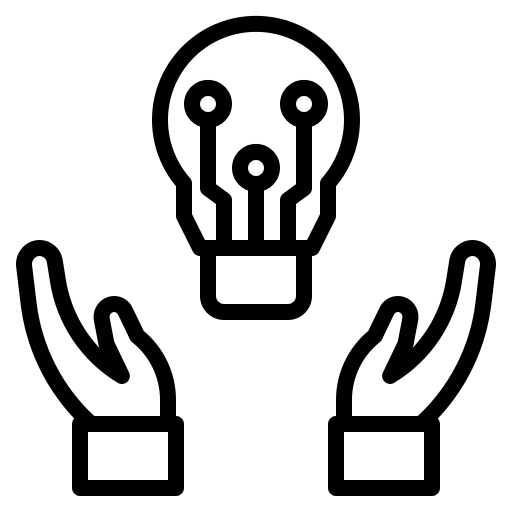
Chances are you’re familiar with the phrase, “the devil is in the details.” This rings especially true for pharmaceutical tech transfer. Missing or inaccurate information will delay production and result in resource waste.
That’s why it’s crucial to prepare a tech transfer package before initiating any next steps. This will help to get everyone on the same page about what is and is not essential to include.
This package should be comprehensive and contain all relevant information related to developing or manufacturing a specific therapy.
What goes in a tech transfer package?
- Raw materials needed
- Manufacturing procedures
- Training requirements
- Past development reports (including information about finished product, deviations, stability, quality review, validation, stability, and environmental conditions)
- Drug packaging and branding instructions (including list of active ingredients, recommended dosage amount and frequency, name of the product, closure or foiling)
- Cleaning processes and procedures
- Facility design details including requirements for equipment, environment, etc.
Tech Transfer Tip #3: Maintain Regular Communication
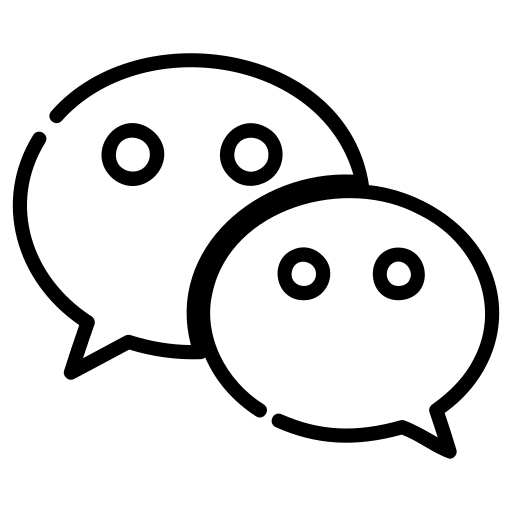
Regardless of where tech transfer is happening — be it during the drug development phases, between sites, during a merger, or to a CDMO, ongoing communication between the sending and receiving organization is key.
You and your partner organization can benefit from regular communication about drug development, production delays, inventory updates, or any quality issues that arise.
By checking in regularly with your supporting organization, you’ll be able to identify potential issues, resolve problems in real time, and accelerate time to market.
Tech Transfer Tip #4: Consider Site Variables
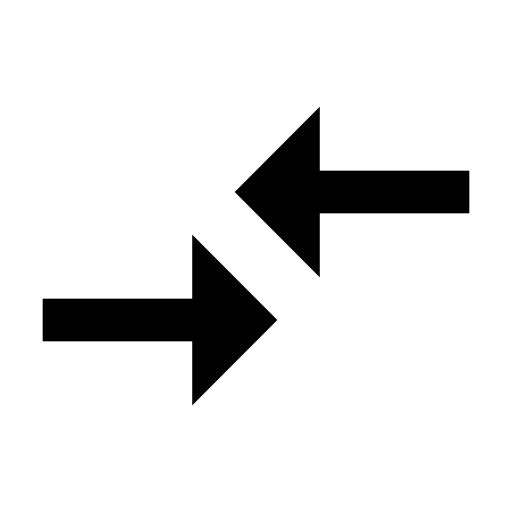
Usually, differences are celebrated… unless we’re talking about drug manufacturing sites. In this case, differences are likely to be a cause for concern.
Site to site variables, including equipment and environmental disparates, can negatively impact drug production. Even minute differences in temperature and humidity can lead to undesired manufacturing complications.
As such, it’s important to consider site-to-site variables such as:
- Knowledge gaps
- Facility differences (equipment, environment)
- Access to and quantity of raw materials
- Documentation processes
- Personnel differences (culture, language, workflows)
Accounting for these types of variables will help you mitigate issues and plan for a seamless manufacturing process. Remember: knowing is half the battle!
Tech Transfer Tip #5: Set Up a TT Team
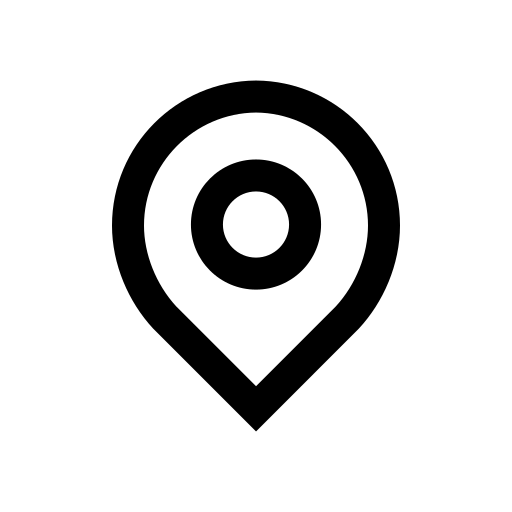
In the pharmaceutical industry, having a tech transfer team is not only expected, it’s essential. Tech transfer impacts the entire drug manufacturing lifecycle, which is why you’ll need a TT team in place at every progression.
This team will coordinate cross-functional requirements, align with external teams and stakeholders, and act as the point of contact.
Your TT team will also set up ongoing checkpoints to verify that:
- Tech and validation batches meet standards
- Regulatory filing submissions are complete
- Scale-up and process optimization are going as expected
- Your goals, including budget and time to market, are being met
Tech Transfer Tip #6: Digitize Your Data
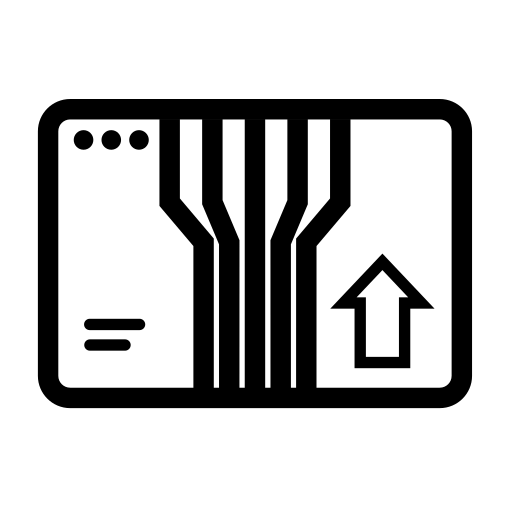
It’s 2022, not 1922 — meaning it’s time to let tech do the heavy lifting for you. Rather than relying on paper-based records that are disparate, hard to decipher, or riddled with transcription errors, you have the option to step away from the paper and level up your data transfer game.
How? By digitizing your data capture and transfer with smart, AI-powered solutions.
Not only will this save you ample time and money, it will also reduce the likelihood of process deviations and delays. Plus, by digitizing your data you’ll streamline the entire tech transfer process — which is a win-win-win scenario for you, your support organization, and patients around the world.
Tech Transfer Tip #7: Connect Your Systems
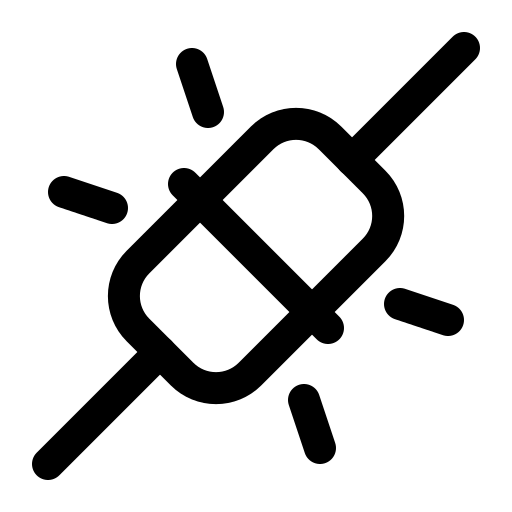
Do you use more than one system to manage your data? If you’re nodding your head “yes,” you’re not alone.
Many pharmaceutical organizations rely on multiple solutions, including manufacturing execution systems, laboratory management systems, and electronic lab notebooks. In many cases, these solutions are disparate and aren’t able to talk to each other.
Using a patchwork of disconnected systems might make you feel like a chicken running around without your head as you try to collect and sync all of the necessary data for your TT package.
Although not all software solutions integrate with each other, it’s worth finding out if your current systems have this capability. If not, consider swapping to cloud-based solutions that can easily share data across locations, devices, and teams.
Full disclosure: it’s never fun to switch your systems when they’re already set up, but the long-term benefits often outweigh the short-term cons when it comes to ensuring your data is connected and easily accessible.
Tech Transfer Tip #8: Protect Your IP
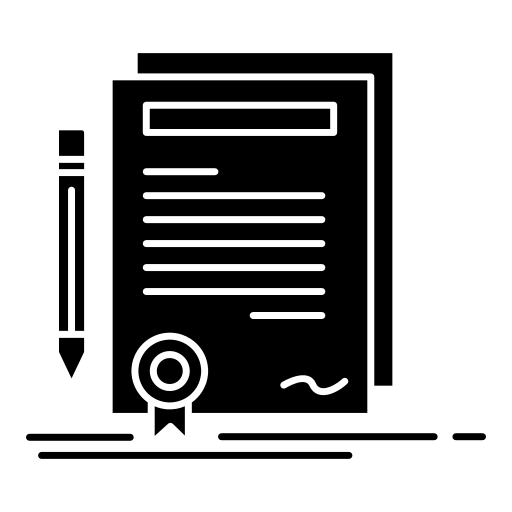
It costs millions (sometimes billions) of dollars to bring a new drug to market. As such, protecting your intellectual property (IP) from infringement during pharma tech transfer is crucial to maintaining a healthy bottom line.
Depending on what phase your TT begins, or the receiving teams or countries, you may need to take steps to protect your IP from infringement before you share information.
You can protect your IP by:
- Patenting your drug processes and recipes
- Registering drug products
- Creating non-disclosure and licensing contracts for employees and partners to abide by
Tech Transfer Tip #9: Create Procedures
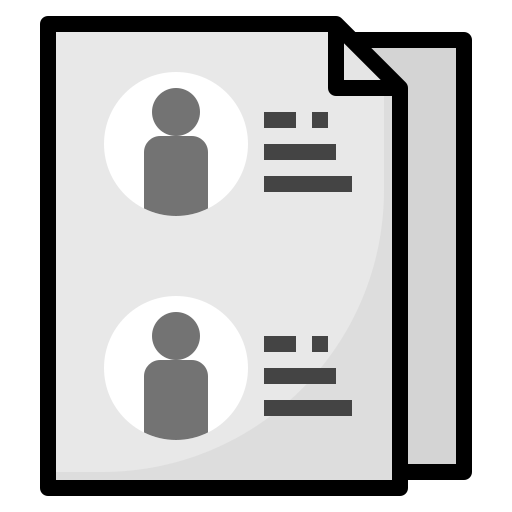
One of the easiest ways to ensure the success of your pharma tech transfer is to co-create formal procedures with your partner(s). These guidelines should outline how the tech transfer process will work, and who will receive and action the information.
Procedures should specify specific steps to take, timelines, and various protocol validations such as equipment, process, and cleaning.
By agreeing to these procedures in advance, you will mitigate any risks associated with the receiving organization misinterpreting how the process should work, or being confused by the information they receive.
These procedures will keep stakeholders informed and accountable throughout drug development and manufacturing. Plus, they will ensure all personnel are adhering to good manufacturing practices (GMP) — regardless of jurisdiction.
Tech Transfer Tip #10: Monitor Changing Regulations
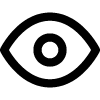
The regulatory bodies that monitor the safety, efficacy, and purity of drugs vary by country. As such, when you start manufacturing at scale, and produce and sell into foreign markets, you’ll need to ensure you monitor changing regulations on an ongoing basis.
This may require you to develop unique tech transfer packages for each country you develop and sell therapies in. If you have a global reach, make sure not to overlook this step as it can cause delays in the production cycle and add unnecessary costs.
Closing Thoughts: Goodbye, TT Headaches!
The pharma tech transfer process may be intricate and complex, but it doesn’t have to be a headache. Instead, you can use the ten tips outlined in this article to streamline tech transfer, reduce resource waste, mitigate process deviations, and accelerate time to market.
Remember, tech transfer isn’t just a process — it’s a living collaboration between you, your employees, and partners.
If you’d like to learn more about how to connect and digitize your systems, check out our Tempo Manufacturing Cloud. It’s a cloud-based solution that we built specifically and exclusively for pharmaceutical organizations. Our top goal? Helping to optimize transparency, accessibility, and reproducibility in tech transfer and throughout the whole drug manufacturing lifecycle.